Metal stamping has been an integral part of the manufacturing industry. It has played a significant role in the production of various items, ranging from household items to industrial parts. Metal stamping involves the use of a die to create specific shapes of metal parts. Drawing die is one of the critical components used in the metal stamping procedure. In this article, we will discuss the use of in-mold rotary cutting process for changing continuous drawing die.
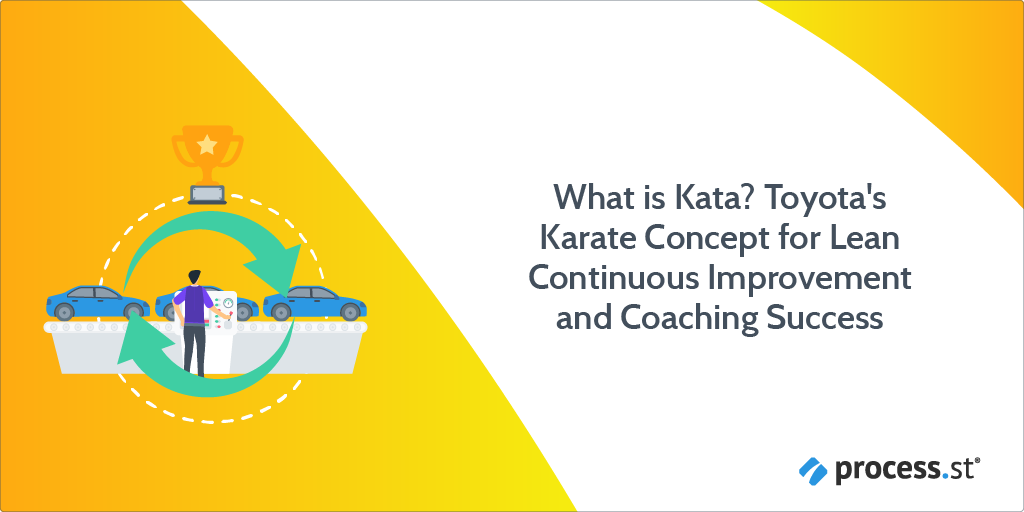
Drawing Die
Before we delve deeper into the in-mold rotary cutting process, let us first talk about the drawing die. A drawing die is a specialized tool that is used to help shape material into specific and desired shapes. The use of the drawing die is particularly common in industries that handle metal stamping, among others. The die is made of tough, durable material, including tungsten carbide, and is designed to efficiently stamp metal plates under high pressure. The quality of the drawing die plays a significant role in determining the quality of the final product.
In-mold Rotary Cutting Process
To ensure that the drawing die is always in perfect condition, manufacturers have developed the in-mold rotary cutting process. This process is designed to change continuous drawing die without the need for removing the material piece from the die. In this process, the drawing die is rotated while the metal material is being pushed through the die to create the desired shape.
The in-mold rotary cutting process is a relatively new technology used in metal stamping. It was developed to solve the difficulties and cost implications of changing the drawing die after every production cycle. The process is incredibly efficient, as it cuts down on production time and ensures a reduction in overall costs.
Advantages of In-mold Rotary Cutting Process
One major advantage of the in-mold rotary cutting process is that it eliminates the need to remove and replace drawing die after every production cycle. This helps to save time, increase efficiency and ultimately reduce costs. With this process, several continuous drawing dies can be set up in a sequence with varying shapes to meet the different production requirements.
Another benefit of using the in-mold rotary cutting process is that it maintains the quality of the final product. The continuous rotation of the drawing die ensures that the material part made through the different drawing dies is seamless, with a smooth surface finish. This ensures that the end product meets the requirements and standards of the manufacturing industry.
Conclusion
In conclusion, the in-mold rotary cutting process has revolutionized the metal stamping industry. By eliminating the need to change drawing die after every production cycle, it saves time and increases efficiency while maintaining product quality standards. Drawing die play a significant role in the metal stamping process, and we must ensure that we maintain them in good condition. The in-mold rotary cutting process offers an efficient solution to this challenge, and we can expect that it will continue to enhance the manufacturing industry.